In the realm of manufacturing and fabrication, Sheet Metal Welding stands as a cornerstone process, vital for creating durable and intricate structures. Let's delve into the various techniques employed in sheet metal welding, exploring the nuances and applications of TIG Welding, Spot Welding, and Carbon Dioxide Welding. TIG Welding: Tungsten Inert Gas (TIG) welding, also known as Gas Tungsten Arc Welding (GTAW), is revered for its precision and versatility in joining thin metal sheets. Utilizing a non-consumable tungsten electrode and an inert shielding gas, TIG welding produces clean and high-quality welds suitable for a wide range of materials, including stainless steel, aluminum, and titanium. This process excels in applications where aesthetics and structural integrity are paramount, such as aerospace components, automotive parts, and architectural features. TIG welding's ability to deliver precise control over the heat input and weld pool makes it indispensable for welding intricate and delicate sheet metal assemblies. Spot Welding: Spot welding is a fast and efficient welding technique commonly used in mass production environments for joining thin sheet metal components. This process employs electrodes to apply localized heat and pressure, creating welds at discrete points along the metal surfaces. Ideal for joining materials with lower melting points, such as steel and aluminum, spot welding ensures rapid assembly with minimal distortion and heat-affected zones. Automotive manufacturing, appliance fabrication, and electronics production are just a few industries that rely heavily on spot welding for its speed, reliability, and cost-effectiveness.
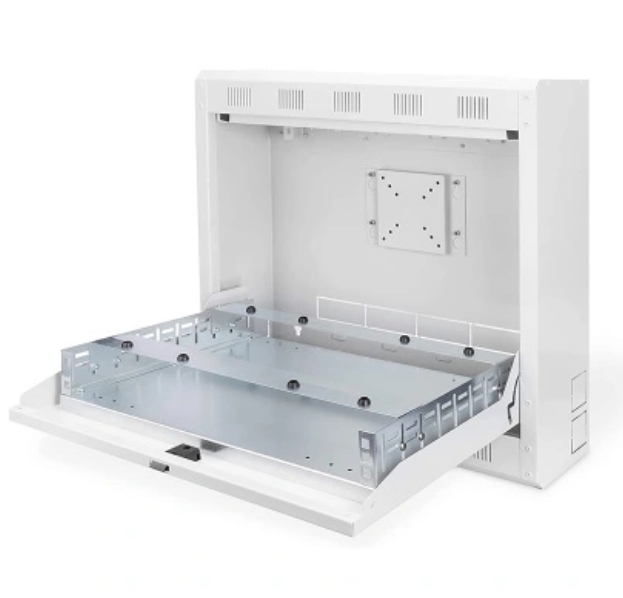
Carbon Dioxide Welding: Carbon Dioxide (CO2) welding, also known as Metal Inert Gas (MIG) welding, is prized for its efficiency and productivity in welding thin to medium-thickness sheet metals. This process involves feeding a consumable electrode wire through a welding gun, which melts and fuses with the base metal under a shielding gas composed primarily of CO2. CO2 welding is highly versatile and suitable for a wide range of materials, including mild steel, stainless steel, and aluminum. Its high deposition rates and minimal spatter make it a preferred choice for industries requiring rapid and robust welds, such as automotive fabrication, shipbuilding, and structural steel construction. In conclusion, sheet metal welding techniques play a vital role in modern manufacturing and fabrication processes, enabling the creation of intricate and durable structures across a myriad of industries. From the precision of TIG welding to the efficiency of spot welding and the versatility of carbon dioxide welding, each technique offers unique advantages tailored to specific applications and materials. As technological advancements continue to drive innovation in welding processes, the future holds promise for further enhancing the efficiency, quality, and sustainability of sheet metal welding operations.